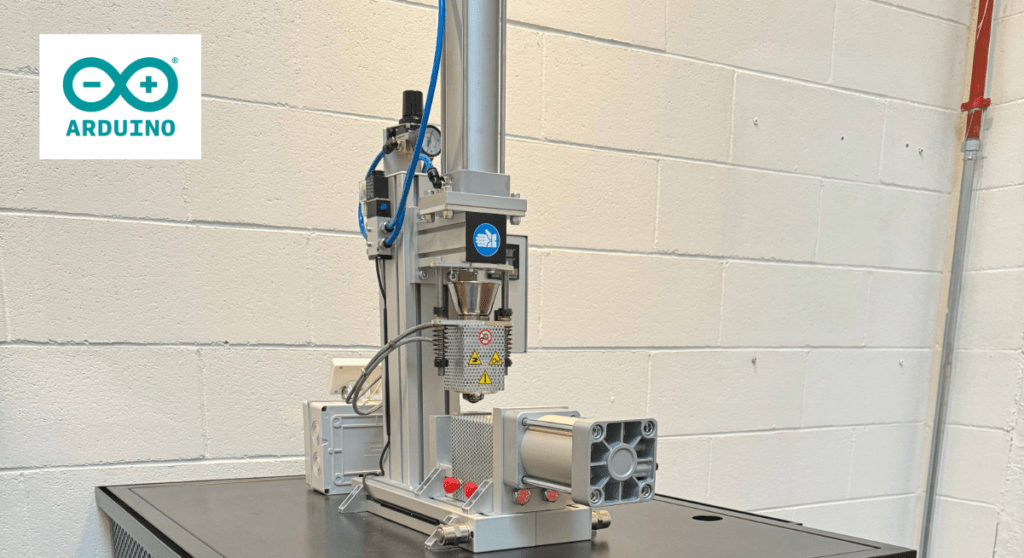
In the rapidly evolving landscape of industrial technology, three interesting trends are intertwining to streamline processes, improve efficiency, and reduce downtime. They are retrofitting, remote control/monitoring, and power metering – and together, they make for a great strategy to upgrade and improve existing machinery, reaping all the benefits of connected things and data analysis without the huge investment of completely new equipment.
- Retrofitting industrial machinery
Retrofitting industrial machinery involves updating existing equipment with modern technology to enhance functionality and performance. It allows businesses to extend the lifespan of their machinery while adapting to evolving industry standards and requirements. - Remote monitoring and control
Remote monitoring and control enable businesses to oversee their operations from anywhere in the world. This capability not only improves operational efficiency but also facilitates proactive decision-making and troubleshooting, ultimately reducing costs and downtime. - Power metering
Power metering involves tracking and analyzing energy consumption. By monitoring power usage, businesses can identify areas for optimization, reduce waste, and lower energy costs, contributing to sustainability efforts and improving their own bottom line at the same time.
Our latest demo showcases the seamless integration of these three crucial aspects into a single solution, using Arduino technology.
The demo in detail
We focused on retrofitting an injection molding machine – a common piece of industrial equipment – with advanced automation capabilities. By replacing the original controller with the Arduino Opta WiFi micro PLC, we transformed the machine into a connected device.
Now, integrating with the Arduino Cloud, users can monitor and control the injection molding machine remotely via intuitive dashboards. This connectivity allows for real-time oversight of production cycles, performance metrics, and equipment status from anywhere with an Internet connection.
Additionally, the Arduino Opta WiFi is equipped with RS485 communication capabilities, enabling seamless integration with an external power meter – in our case, a Finder model. This provides valuable insights into energy consumption, production output, material usage, and equipment health.
The collected data is then analyzed through dedicated dashboards, offering information about operational efficiency and potential issues. By leveraging this data, businesses can proactively schedule maintenance and repairs, minimizing downtime and optimizing production processes.
Retrofitting for a connected future
Many businesses today can retrofit existing machinery to embrace the benefits of connectivity and automation. Our demo provides a practical example of how common industrial equipment can become smarter, more efficient, and easier to manage. From remote monitoring and control to power metering and predictive maintenance, retrofitting offers a sustainable way to modernize industrial infrastructure.
Unlocking potential across industries
Moreover, the versatility of Arduino’s open-source ecosystem ensures that this solution can be adapted and applied to a wide range of existing machines and equipment, enhancing their operation effectively – whether in manufacturing, logistics, or any other industry relying on machinery.
To learn more about how you can leverage Arduino technology to upgrade your infrastructure and achieve tangible results, contact us today. Let us help you unlock the full potential of your industrial assets with practical, cost-effective solutions.
The post Arduino Cloud and Opta WiFi make an injection molding machine connected and smart appeared first on Arduino Blog.